Over the past 15 years the use of lasers has become more and more widespread in the industry. The use purposes of the lasers are multiple, amongst others they include: scanning, detection, diagnosis, explosion, cutting & dissection, data transfer and many more. Accordingly, the variety of available laser models and laser manufacturers makes the task of choosing the right laser for our optical application a challenge even when we know exactly what our requirements for our laser unit are, according to our technical budget and initial system requirements.
I will try to give, from the optics point of view, a few tips as to what’s important when defining laser requirements for our system and why. I initially planned this post as a sole optics, but as I wrote it I realized that quite a few subjects were a systematic overview of the laser system and eventually it became a mix of System and Optics which is exactly the way I always like to think of things .
When we approach a laser based system there are a few parameters that we must give our attention to when we formulate our requirements for a laser. I am not going to thoroughly explain each terms’ full meaning (that would require much more than a single post), but rather I will mention it should be there and why.
Center Wavelength and Line-Width
The center wavelength is a basic parameter in a laser system which in simple terms is what “color” we require in [nm] (“color” because it may be invisible light). Bear in mind that in quite a few laser manufacturing technologies the center wavelength will have its tolerance which can shift up to 10nm or even more between units. We refer to the laser’s center wavelength because narrow as it may be, the spectral output of a laser always has some breadth called line-width which may also be in the order of 10nm. BTW there are applications where even the Power Spectral Distribution within the line-width are of importance but these are certainly extreme cases so we will leave these out of our discussion. In addition, the physics of a laser unit usually strongly depends on environment characteristics which may shift the center wavelength and line-width during operation such that the stability during operation has also to be defined. Good or bad depends on your system’s sensitivity to these parameters.
An example for requirement:
Center wavelength 450nm +/- 1nm Center wavelength stability during operation +/-0.1nm Line-width < 2nm
Note: there are also “white lasers” or super-continuum lasers where these light sources have all the characteristics of a laser but with an emission of a wide range of wavelengths. Obviously, center wavelength is irrelevant in these kind of lasers, and then you’d have to define the whole range of wavelengths according to your need, but let’s be frank, when you need one of these, you probably already know how to define it .
Pulse or CW Mode
The need for pulse or continuous wave (CW) mode is a characteristic somewhere between System and Optics. If for example we have an imaging system that cannot be synchronized with our laser pulses we would require the laser to be CW. Obviously, if the wavelength required could be manufactured only in pulse mode there is not much we could do about it.
When defining a pulse mode laser we must provide our requirements for the pulse length, the duty cycle of the pulses and the rise\fall time of the pulse signal. Remember to clearly define the rise\fall time: some define the rise time from 0 to 66% of the target signal and some from 0 to 90%. Make sure you all speak the same language here. We can also manipulate a pulse mode around such that it would be almost CV (quasi-CW) where the duty cycle is close to 100% and our opto-electronic collection system, the sensor for example, is much slower than the pulses. For example a 100ms exposure time camera frame is indifferent to a 10kHz pulse laser, for which it would seem as if it were a CW laser. Example for pulse laser requirements would look like this:
Laser mode – Pulse mode Minimum\Typical\Maximum pulse length – 1\2\3 ms Minimum\Typical\Maximum duty cycle – 25%\50%\75% Rise time from 0 to 85% target signal < 75us Fall time from 85% target signal to 0 < 120us Stabilization time into range +/-10% target signal < 150us
For the different pulse timing requirements please refer to the following sketch which visually displays each definition
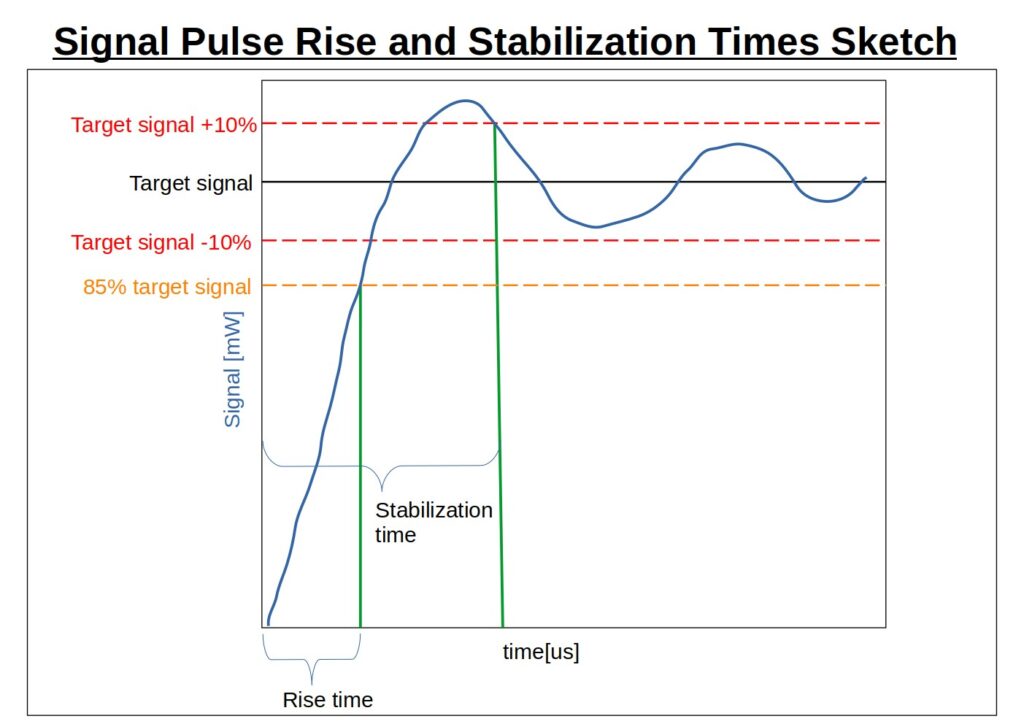
Total Power
The total power of the laser has a lot of impact over the optical system, optical design wise and system design wise. If we need a 3mW power of green laser for our application a 10mW laser with attenuation would probably do the trick engineering wise, but we then have to take into account that the laser safety class has gone up (in our case from class IIIa to class IV) and we may need to add protective measures to the system or the user, which will have its impacts. Furthermore, having a class IV optics inside your system requires all the optics to be compatible with this power level (Laser Induced Damage Threshold – LIDT – change). Of course, we have to define the stability of the power. For example:
Total Power 50mW +/-5%
Polarization
First, in this context polarized = linearly polarized. In some laser emission technologies the light emitted is polarized to begin with, in some technologies it can be forced to a certain polarization and in some technologies it cannot be done at all (other than inserting a polarizer and lose 50% of the light). It is good to know if we need polarized light to begin with. Maybe there are models that come inherently with polarized light and thus save us the headache of taking into account its polarization down the light path in our system. When defining the polarization we must state which is the allowed maximum ratio between the ordinary and the extra-ordinary polarization in the output.
Polarized light
Polarization ration 1:100
Free Space and Fiber Coupled
There are two main methods to emit the laser from a laser source: free space and fiber coupled. Your definition for one or the other would depend on your optical architecture and detailed design. Bear in mind that not every type of laser could be fiber coupled (at least not efficiently) so that may force your optical design to a certain architecture. When defining a fiber-coupled laser we should say if the fiber is multi-mode or single-mode and whether it is polarization maintaining fiber.
Beam Diameter \ Spot Size
Even if you are dealing with a fiber coupled laser, you emit it eventually somewhere for your own purposes. Either way you would want to make sure to have the final beam diameter defined, even if you do not hand it in as a requirement for the laser vendor. It is a good practice mainly to catch improbable situations for example if you had an IR 2500nm wavelength and you system required a 2u spot size you would probably have to stop right there and recalculate all your technology from scratch. A diameter requirement would look something like this:
Beam diameter for 90% of the energy < 10um
Power Spatial Distribution \ Beam Shape
There are applications where the actual beam shape makes a difference. In such cases these should be defined and discussed upon with the laser vendor. The laser manufacturer should know very well what the beam shape of his lasers is and give you a detailed input whether what you are asking for is even possible. In many cases you can reshape the beam with optical elements but if these could, a-priory, be integrated inside the laser module it would be better systematically.
Beam shape – Gaussian beam
Beam Quality or M2 (M-Squared) –
Again, the exact explanation for what M2 is is outside this post’s context, let’s say it is a way to measure how “good” the laser beam is, and how close it is to a perfect Gaussian, so in fact it is somewhat a subsection of the beam shape above. The closer it is to 1 the “better” the beam is. Please remember that good or bad is application dependent so when quality is concerned I keep the subjective definitions in double quotes.
M2 < 15
Divergence Angle
We sometime have to carry the laser beam over a long distance in free space or transparent material without the technical possibility to have focusing optics in the path. The divergence angle in these cases is crucial for keeping the energy inside our beam diameter. Note that in the optical design we can adjust the divergence angle to the required value, however this is something you would want to plan ahead and not find out that you are required to add a focusing lens after integrating the laser inside the optics.
Beam divergence angle < 1mRad
Beam Waist
I am not going to cover what laser beam waist is, but for the sake of those who are unfamiliar with this term it is a geometrical property of the laser beam propagation. In many cases the beam waist requirements are defined alongside with the divergence angle of the beam. The different definitions of beam waist differ between vendors so I keep this paragraph without an example.
Coherence Length
Coherence length, as the name implies, is the distance for which a laser beam keeps it coherence properties. If that sounds a bit obscure, I apologize. I promise to have a post dedicated for light coherence. In any case, when your application uses coherence (or on the other hand suffers from coherence) a minimal\maximal coherence length should be mentioned in you requirements:
Minimum coherence length 1000mm
Turn On and Warm-Up Time
This is a systematic requirement. If we have a laser that has to go into a hospital emergency room we cannot have the laser warm-up time to be 30 minutes.
Warm-up time < 120 seconds
Mechanics: Dimensions & Weight and Cooling
It is really nice we’ve found a lovely laser unit that does the job for us but if it does not fit inside our machine or it is too heavy there’s not much use for such a laser. In addition most of the lasers out there require cooling, either passive or active. This is something that should be communicated with the laser vendor since it may be a make or break for the system’s compatibility with the laser. If active cooling is required, it should mention exactly the amount of hear needed to be evacuated in BTU or Watt or any other measurement unit.
Max laser unit dimensions (H, W, D)[mm] (200, 200, 250)
Max laser unit weight 1500g
Cooling: passive cooling \ laser unit inherent cooling
Power Supply
Another systematic requirement that may affect the optical design. If we have in our system only 12V\2A DC power supply available, this is something we should communicate early in our search for a laser unit. You may find between the lines that combining the power supply and the cooling requirements together may give us a hidden requirement for the laser’s efficiency, but that is usually not a direct requirement for the laser.
Power supply 5V\3A DC
Command Interfacing \ Driver \ Control
Some laser units come out of the box with an inherent driver and a control unit and with their own interface whereas some come without anything save for 2 wires and for some you may define whatever interface and control you want and the vendor will have it manufactured for you. Usually for prototypes you would choose the laser with the driver attached to it to save the time of interfacing to the laser, but each system has its own ins and outs. In any case, the command interface should be clear with the vendor. I will use a pinout example here, but here there is no template because the interfacing options are endless.
Interface – 4pins pinout: pin1 vcc, pin2 gnd, pin3 comm1, pin4 comm2
Target Price
Last but not least. Do not start negotiating the technical details with a laser vendor that has an initial unit price for mass production of 100X your target price. It will be a waste of both your efforts. I had negotiated the technical details of a laser just to realize that it was 5 times the price we budgeted for a unit.
Target price US$1000 per unit for 1000 units/year
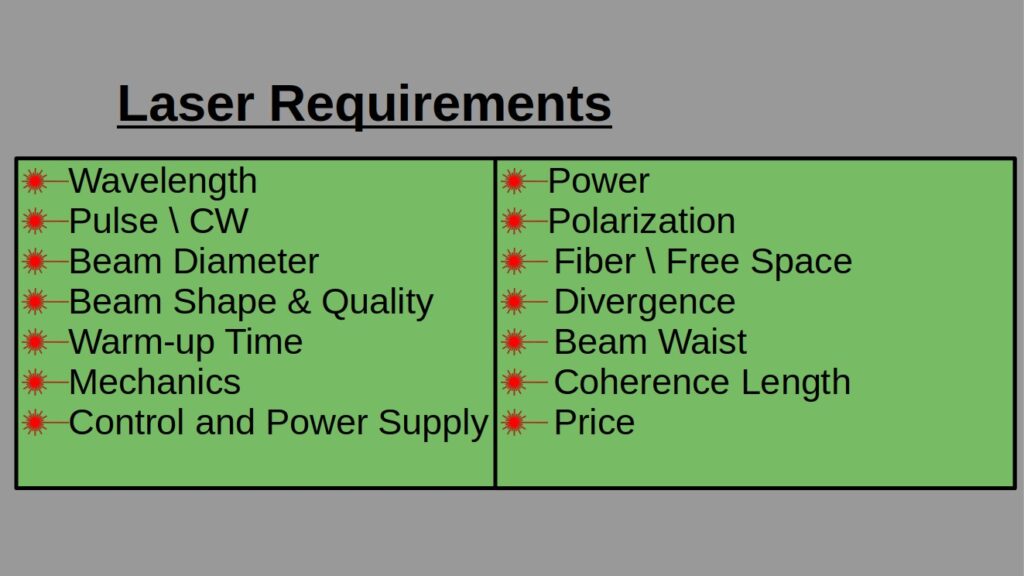
I think that about covers it for now. There are probably more aspects to be considered but that’s the gist of it. I truly hope you find this useful next time you look up a new laser for your system. Remember that even if you are indifferent to some of the parameters described above you should add them eventually to your specifications with the vendor. It will make your life easier to follow up on changes with the vendor when going into mass production.